How To Select The Good Raw Materila For Making High Quality Toilet Paper?
Throughout your life, you will use about…
This much toilet paper.
But how is it made?
Why did we choose toilet paper?
We will take you to study this small miracle of human creativity.
Simply put, turning tall, hard trees into soft, white toilet paper in your hand requires four major steps: converting trees into pulp, further processing the pulp, spraying and drying it into tissue paper parent rolls, and finally rolling and cutting it into toilet paper roll.
Although it sounds simple, each step has some intricacies we might not be aware of.
Step 1: Making Pulp Material
Despite the many types of toilet paper, the pulp material is the main factor determining its quality and price. National regulations require all toilet paper and tissue packaging to clearly state the type of raw material used. We created a four-quadrant chart categorizing the raw materials. With this chart, you can quickly understand the raw materials on the packaging and not be misled by merchants.
At the top is virgin wood pulp, and at the bottom is recycled pulp.
Virgin pulp is made entirely from new, natural plant materials. Note these three keywords: entirely, new, natural plants. Recycled pulp, as the name implies, is made from recycled materials. What recycled materials?
According to national standards, recycled pulp can only use recovered paper prints and white paper edges as raw materials; it cannot use discarded household paper, medical paper, packaging paper, etc.
Recycled pulp toilet tissue is generally cheaper but of lower quality, prone to shedding dust and lint. You rarely see such products in supermarkets. Due to the risk of fluorescent substances and heavy metals in recycled pulp materials, this type of toilet paper is not recommended for facial or mouth use.
In addition to virgin and recycled concepts, bath tissue raw materials are divided into wood pulp and non-wood pulp, such as bamboo pulp. In recent years, pulp from wheat straw, reeds, and bagasse has also been used. So, the horizontal axis can be labeled as wood pulp and non-wood pulp.
Some merchants use deceptive marketing concepts to mislead consumers, such as “pure wood pulp,” which sounds high-end, but virgin wood pulp mixed with recycled pulp can also be called pure wood pulp. Similarly, “pure virgin pulp” might include both wood and non-wood pulp.
If you are unsure about these concepts, just look for the term “virgin wood pulp.”
Step 2: Processing Pulp into Paper Pulp
Directly making paper from initially processed pulp would feel like sandpaper. To make toilet paper soft enough, the pulp must undergo a pulping process. This process changes the fiber shape, controls the ratio of long and short fibers, and delivers a gentle tactile experience. Factories use machines like pulpers and refiners to complete this process. Wood pulp is mixed with water and then goes through processes like de-sanding, refining, and dispersion.
This process further cuts the pulp fibers and turns them from coarse, straight fibers into broom-like structures with many fine fiber branches. This process is called fibrillation. Under a microscope, the fibers look like this before beating and like this after beating.
The processed pulp fibers become not only soft and fluffy but also form a gel-like substance when immersed in water, making it easier to bond together into a sheet of paper. Different raw materials produce virgin pulp with various internal chemical compositions and fiber structures, resulting in different paper properties.
For example, wood pulp fibers from trees like pine and fir are long and thin, making the paper stronger and harder to tear. Eucalyptus and birch, being broadleaf trees, have short and thick fibers, making the paper soft and absorbent. After beating, manufacturers mix long and short fibers in proportions of 3:7 or 4:6, so the final toilet paper is both soft and absorbent yet resistant to tearing during use.
To make bathroom tissue flushable, sodium carboxymethyl cellulose (CMC) is added to the pulp. It forms a fiber network with the plant fibers but quickly dissolves in water, breaking the wet toilet paper from the inside and preventing clogging.
Step 3: Making Semi-Finished Paper
In this step, the pulp is sprayed evenly onto a mesh surface through pressurized nozzles, then pressed and dewatered. It is then dried further in a drying cylinder, where the high temperature also sterilizes it. When the moisture content is about 93%, an important step in toilet paper production occurs: creping.
The paper sticks to the drying cylinder and slides to the blade, where it is creped into fine wrinkles, like the wrinkles time carves on your face. Wrinkles are essential for toilet paper. The blade can disrupt the bonding between fibers, making them more loosely connected. After creping, the paper’s longitudinal elongation increases eightfold, its thickness triples, and its stiffness decreases by 38%, making the paper more elastic, thicker, more absorbent, and softer.
This process significantly impacts the final quality of the toilet paper. If the blade is not strong and stiff enough, it will frequently cause paper jams. If the paper stays on the blade too long, small wrinkles turn into large wrinkles. Generally, the blade-to-drying cylinder angle is between 18 and 30 degrees.
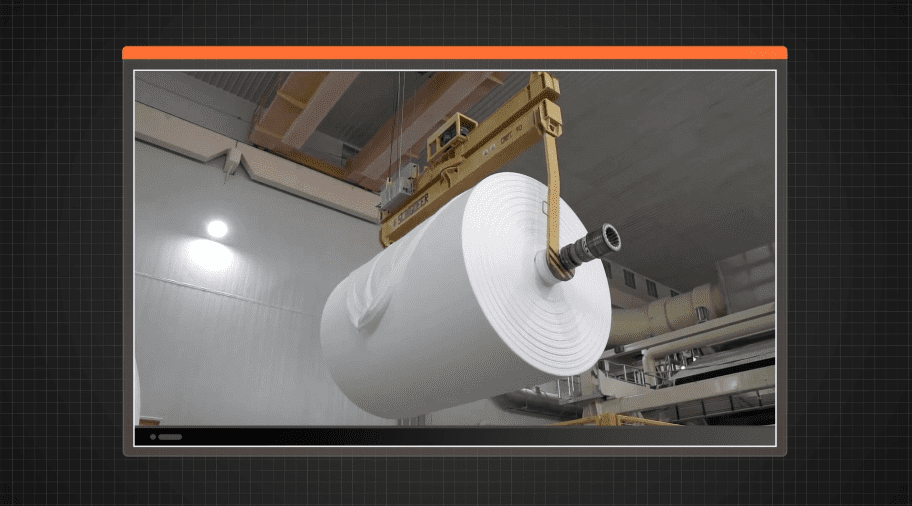
The cold, hard metal, calculated with precise angles, can create fine and even wrinkles in the paper. Even a slight change can affect the final user experience. The paper produced at this stage is rolled into tissue jumbo rolls, some weighing hundreds of kilograms or even several tons. A 200 kg jumbo roll can supply a family of three for ten years.
Step 4: Finished Product
Single-layer semi-finished paper is too thin to give us a sense of security. So, manufacturers load several tissue mother rolls onto a machine and roll them into multi-layer finished toilet paper. Generally, three to four layers of toilet paper allow you to save paper while preventing your fingers from touching unwanted substances.
To make tearing easier during use, perforated lines are added. Having or not having a core is not a marker of high or low quality; it just suits different usage conditions. Both types are cut into small rolls and packaged for sale.
After this long journey, a pine tree that has weathered the Scandinavian storms finally meets a fast-growing eucalyptus basking in South American sunshine. Through trials of water and fire, they merge completely, becoming white, light, and soft. They embrace each other and walk towards their glorious end together.
This concludes our exploration of toilet paper. We will provide links to related papers and materials at the end for further research. Lastly, there are three points to remind everyone:
Bacterial colonies: The standard for toilet paper is lower than for tissues, so national standards require toilet tissue to be labeled “for toilet use.” Using toilet paper to wipe your mouth is unhygienic.
Dust shedding: Toilet paper should not shed more than 0.5% of its weight, while tissues should not shed at all. Therefore, people with allergic rhinitis should avoid using toilet paper to wipe their noses as it might worsen their condition.
Water-soluble fibers: Unlike toilet paper, tissues do not contain water-soluble fibers, making them more likely to clog toilet paper. If you temporarily use facial tissues instead of toilet paper, it’s best to throw them in the trash.