How to make the tissue jumbo roll from the virgin wood pulp board?
Tissue jumbo rolls are large reels of tissue paper that are used to produce various finished products such as toilet paper, paper towels, napkins, handkerchiefs and so on. They can be made of different kinds of pulps, such as virgin pulp, recycled pulp or mixed pulp. In this article, we will focus on how tissue jumbo rolls are made of virgin wood pulp board.
Virgin wood pulp board
Virgin wood pulp board is a type of raw material that is derived from wood chips of softwood and hardwood trees. It is called virgin because it has not been used or recycled before. Virgin wood pulp board has a high quality and purity, which makes it suitable for producing soft and strong tissue paper.
Tissue jumbo roll production process
The production process of tissue jumbo rolls from virgin wood pulp board can be divided into four main stages: pulping and refining, paper making, winding and converting.
Pulping and refining
The first stage is to transform the virgin wood pulp board into a pulp paste that can be used for paper making. This involves the following steps:
– The virgin wood pulp board is cut into small pieces and mixed with water and chemicals in a digester. The mixture is cooked under high temperature and pressure to dissolve the lignin (the glue that binds the wood fibers together) and separate the cellulose fibers.
– The cooked pulp is washed and screened to remove the impurities and the remaining lignin. The washed pulp is then bleached with chlorine dioxide or hydrogen peroxide to whiten it and remove any traces of color.
– The bleached pulp is refined by passing it through a series of discs or cones that beat and fibrillate the fibers, making them more flexible and absorbent.
Paper making
The second stage is to form the refined pulp into a thin sheet of tissue paper. This involves the following steps:
– The refined pulp is diluted with water to form a slurry that has about 99% water and 1% fiber. The slurry is sprayed onto a moving wire mesh screen that drains the water and forms a wet web of tissue paper.
– The wet web is pressed between two felt rollers to remove more water and increase the strength of the paper. The pressed web is then dried by passing it through a series of heated cylinders or a hot air hood that evaporates the remaining water.
– The dried web is creped by scraping it off with a metal blade at an angle. This creates small wrinkles on the surface of the paper, which enhance its softness, bulkiness and stretchability.
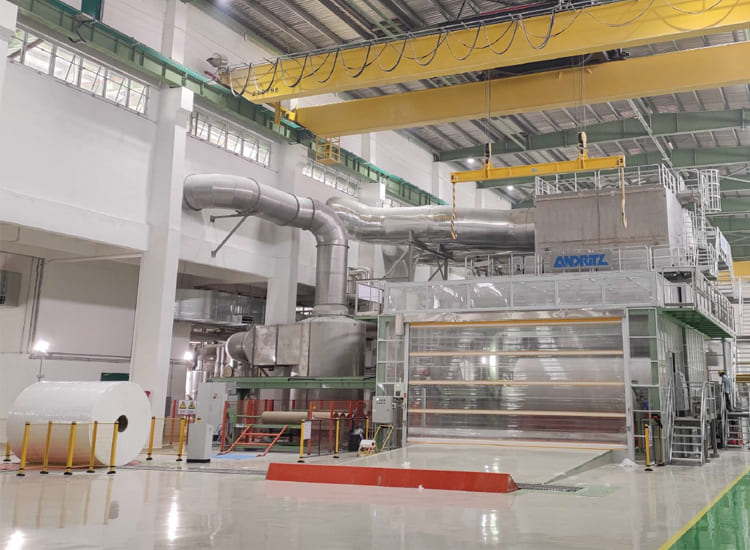
Winding
The third stage is to wind the tissue paper into large reels called parent rolls or jumbo rolls. This involves the following steps:
– The creped tissue paper is wound around a steel core at a high speed. The winding tension is controlled by a device called a rider roll that presses on the paper roll.
– The wound paper roll is cut by a slitter into smaller widths according to the specifications of the customers. The slit paper rolls are then transferred to a reel stand that holds them until they are ready for converting.
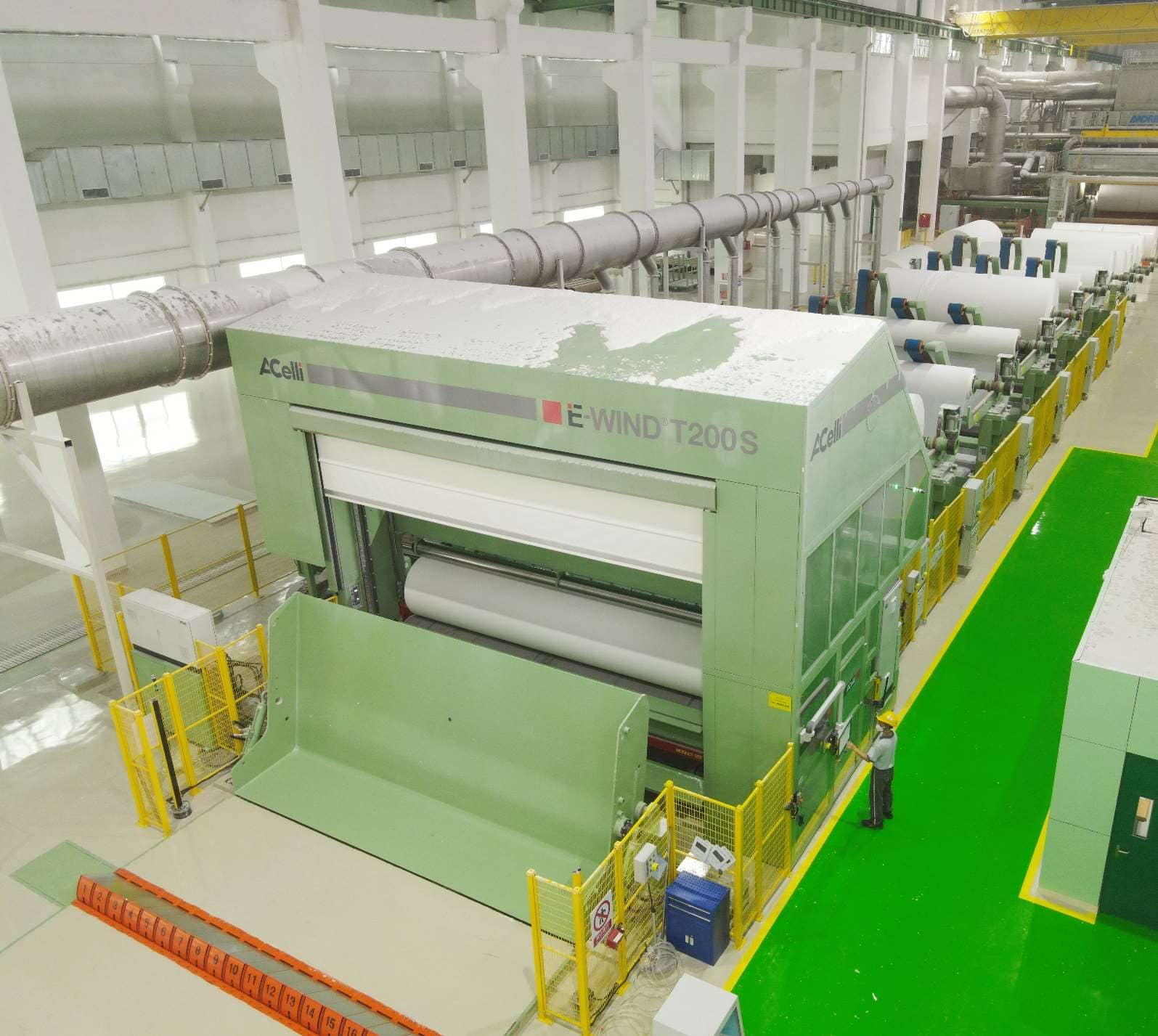
Converting
The fourth stage is to convert the jumbo rolls into finished products that are ready for sale. This involves the following steps:
– The jumbo rolls are unwound and fed into a converting machine that performs various operations such as printing, embossing, perforating, rewinding, cutting and packaging.
– The converting machine can produce different types of finished products such as toilet rolls, paper towels, napkins, handkerchiefs etc. depending on the configuration and settings.
– The converted products are then packed into bundles, cases or pallets and shipped to the customers.
Machines and equipment used for tissue jumbo roll production
The production of tissue jumbo rolls from virgin wood pulp board requires various machines and equipment that perform different functions and tasks. Some of the main machines and equipment used are:
– Digester: A large pressure vessel that cooks the wood chips with water and chemicals to produce pulp.
– Washer: A device that washes and cleans the pulp by removing impurities and lignin.
– Bleacher: A device that bleaches the pulp by adding chlorine dioxide or hydrogen peroxide to whiten it and remove any traces of color.
– Refiner: A device that refines the pulp by beating and fibrillating the fibers to make them more flexible and absorbent.
– Headbox: A device that distributes the diluted pulp slurry evenly onto the wire mesh screen for paper making.
– Wire section: A part of the paper machine that consists of a wire mesh screen that drains the water from the pulp slurry and forms a wet web of tissue paper.
– Press section: A part of the paper machine that consists of two felt rollers that press the wet web to remove more water and increase the strength of the paper.
– Dryer section: A part of the paper machine that consists of heated cylinders or a hot air hood that dry the pressed web by evaporating the remaining water.
– Creping unit: A device that crepes the dried web by scraping it off with a metal blade at an angle to create small wrinkles on the surface of the paper.
– Winder: A device that winds the creped tissue paper around a steel core at a high speed to form jumbo rolls.
– Slitter: A device that cuts the wound jumbo rolls into smaller widths according to customer specifications.
– Reel stand: A device that holds the slit jumbo rolls until they are ready for converting.
– Converting machine: A device that converts
the jumbo rolls into finished products by performing various operations such as printing, embossing, perforating, rewinding, cutting and packaging.
Summary
Tissue jumbo rolls are large reels of tissue paper that are used to produce various finished products such as toilet paper, paper towels, napkins, handkerchiefs etc. They can be made of different kinds of pulps, such as virgin pulp, recycled pulp or mixed pulp. In this article, we focused on how tissue jumbo rolls are made of virgin wood pulp board.
The production process of tissue jumbo rolls from virgin wood pulp board can be divided into four main stages: pulping and refining, paper making, winding and converting. Each stage involves different steps, machines and equipment that transform the raw material into a final product.
The following table summarizes the main stages, steps, machines and equipment used for tissue jumbo roll production from virgin wood pulp board.
Sure, here is a chart summarizing the main stages, steps, machines and equipment used for tissue jumbo roll production from virgin wood pulp board:
Stage | Steps | Machines/Equipment |
Pulping and refining | 1. Debarking and chipping 2. Digestion and washing 3. Bleaching and screening 4. Refining | 1. Debarker and chipper 2. Digesters, washers and screens 3. Bleacher and cleaners 4. Refiners |
Paper making | 1. Preparing the stock 2. Forming the sheet 3. Pressing the sheet 4. Drying the sheet | 1. Stock preparation equipment 2. Fourdrinier machine 3. Press section 4. Dryer section |
Winding | 1. Slitting 2. Rewinding 3. Cutting | 1. Slitter rewinder 2. Rewinder 3. Log saw |
Converting | 1. Perforating 2. Embossing 3. Cutting 4. Packaging | 1. Perforating machine 2. Embosser 3. Log saw \ 4. Packaging equipment |
Related Topics
– Bamboo Pulp or Virgin Wood Pulp: Which One is More Suitable for Tissue Paper Production?
– A Comparison of Virgin Wood Pulp and Bamboo Pulp for Tissue Paper Properties and Performance
– The Advantages and Disadvantages of Using Virgin Wood Pulp or Bamboo Pulp for Tissue Paper Products
– How Virgin Wood Pulp and Bamboo Pulp Affect the Environmental Impact and Cost of Tissue Paper Production
– Virgin Wood Pulp vs Bamboo Pulp: A Critical Analysis of Their Differences and Similarities for Tissue Paper Applications